Innovation Award 2023
Category criteria
- This category is open to individuals, teams or businesses making a big impact with an innovation.
- The innovation could be a new product, service or process or it could be an innovative use of an existing product, service or process.
- The judges will be keen to find out about the intellectual processes which gave rise to the design and development of the innovation.
- The judges will also want to know how innovation is handled within the culture of the company and will welcome nominations from businesses that have innovation at the core of their ethos.
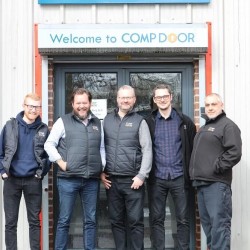
Comp Door
Innovation Award entrant
A Staffordshire door manufacturer reported revenue of £4.8 million in its first year and is on track for revenue of up to £10 million for year two. The projected turnover for 2024 to 2025 is £15 million.
Comp Door, based in Chesterton, Newcastle-under-Lyme, had just two staff when it was launched in November 2021 and now has a team of 49.
Comp Door’s Technical Director, Pierre Mifsud, said: “The growth we’ve seen during Comp Door’s short life is a testament to our team’s dedication to constant improvement and I’m so proud of how we have been able to achieve our ambitions through consistent hard work and innovation.
“Comp Door’s implementation of the Portal system in particular has been an absolute game changer with regards to our ordering and manufacturing efficiency, and it has already proven itself to be a reliable support mechanism for future business developments, such as new ranges or any major expansion to our operations.”
The Portal system allows customers to design, order and track custom orders in their own time and from the comfort of their own home or office – eliminating the need for trips to the showroom to meet with a designer and time-consuming queries chasing the status of their order.
Not only does this increase order capacity and the rate they can be processed, it enables Comp Door to streamline processes because it simplifies tracking, shares how many ongoing orders are being made at all times, saves paperwork and maximises profitability.
The Portal now takes around 95% of orders, meaning the potential for human error is almost completely eliminated.
In May 2023 the company launched its new Discovery range of doors.
Pierre Mifsud said: “We knew there was increasing demand for European-style doors that suited new, modern houses. We also knew that these demands weren’t being met without quality and durability being compromised in the process.
“At Comp Door, we don’t cut corners – instead, we are always thinking of new ways to innovate and improve our service offering, and in doing so, lead the industry into its new phase of evolution.”
Comp Door has entered the Growth and Innovation categories of the Staffordshire University Business Awards.
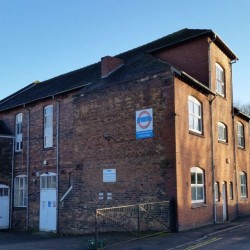
Promtek Ltd
Innovation Award entrant
A second-generation, family-owned business, Promtek Ltd was founded in the 1970s but is very much in the 21st century when it comes to innovation and working practices.
Based in Brindley Ford, the automation technology company is constantly innovating and adapting to meet the needs of its customers in the digital era.
Sustainability is at the core of Promtek’s strategic approach, with a strong focus on achieving net carbon zero and embracing sustainable practices.
It’s a strategy that’s paying off as revenue has increased by 28% year on year.
Promtek has a longstanding relationship with Staffordshire University to offer undergraduate placements and graduate recruitment, as well as opportunities to accelerate its product innovation ideas. This includes funding a collaboration with the University on the first Staffordshire Advanced Manufacturing, Prototyping and Innovation Demonstrator (SAMPID) project to explore the use of robotics in ingredient handling applications.
The company prioritises its employees, fostering a culture of teamwork, creativity and personal growth. The Promtek workforce has grown by 20% this year, with a diverse team from the UK, South Africa and India.
Managing Director Charles Williams said: “We are deeply committed to making a positive impact on our community through various corporate social responsibility initiatives. This includes supporting local charities, championing environmental sustainability and actively participating in community events.
“Our belief in giving back extends to initiatives such as piloting talent development schemes, sponsoring the Port Vale Foundation Africa mission, providing work experience for high school students and offering local work placements and apprenticeships.
“We understand the importance of being a responsible corporate citizen and strive to make a meaningful difference in the lives of those we serve.”
The company won several awards last year including its Storaweigh software receiving the Food Processing Award, an Apprentice of the Year Award from Shapa and a gold employer certificate from Next Gen Makers Kitemark for its apprenticeship scheme.
To expand its global presence, Promtek has established the Promtek Africa office, where it has recruited a team of four professionals from the region.
Charles said: “This strategic move empowers us to deliver our advanced technology to manufacturers in Southern Africa and beyond, broadening our customer base and making a significant impact in the global market. Our presence in Southern Africa underscores our unwavering commitment to innovation, customer satisfaction and international growth.”
He added: “Winning an award at the Staffordshire University Business Awards would be a tremendous honour and a testament to our unwavering commitment to excellence, innovation and community engagement.
“It would validate our tireless efforts and inspire us to continue pushing the boundaries, setting new benchmarks and positively impacting both our industry and the wider community.”
Promtek has entered the Small Business of the Year and Innovation categories of the Staffordshire University Business Awards.
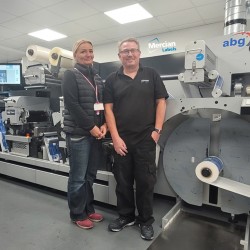
Mercian Labels
Innovation Award entrant
A Staffordshire label manufacturer has an innovation that can increase productivity by as much as 74% and which it believes will revolutionise its industry.
Mercian Labels, based in Burntwood, has spent six years perfecting workflow automation with the aim of significantly reducing job changeover times, minimising material waste, improving productivity and freeing up operator time.
On a test run in September 2022 a job which would previously have taken nearly six hours was completed in one hour and 46 minutes.
Dr Adrian Steele, Managing Director of Mercian Labels, said: “This has been a six-year journey, but the results are outstanding for us as a business, for our customers, for the environment and potentially for the whole industry.
“The automated workflow doubled our production speed and significantly improved productivity, freeing up our team to focus on improvements in other areas.
“Now the new systems and technologies are happily running on a daily basis within our business, our team are already looking at our next innovation to further improve customer satisfaction, protect the environment and maximise the benefits to our community and the economy.”
Back in 2016, as the company approached its 50th anniversary, the 57 staff were asked to suggest innovations that might add value, reduce costs, minimise waste and save time.
One area that stood out was that most labels, once printed on a large reel, then needed to be cut down to the right width and length and fitted on the right sized cardboard core to suit the end user’s requirements.
This required a lot of machine set up time for each job, created additional waste and required highly skilled and experienced operators, who themselves were becoming increasingly difficult to find.
So Mercian Labels set out on what was to become a six year project to create something that had never been done before in its industry, workflow automation.
Mercian Labels has entered the Innovation Award category of the Staffordshire University Business Awards.
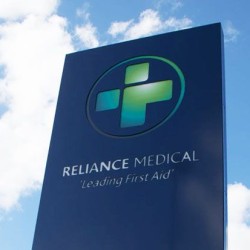
Reliance Medical Ltd
Innovation Award entrant
The UK’s leading trade-only manufacturer of first aid and medical supplies, Talke-based Reliance Medical is on track for a turnover of more than £30 million this year and has a new innovation that will remove the need for more than 3.4 million plastic bottles every year.
The company, which is on target for a £50 million turnover by 2025, also recently won an order to supply 20,000 lifesaving defibrillators for public buildings around the UK.
In late 2022 Reliance Medical launched Aura3, a range of 100% recycled and recyclable first aid kit boxes that will remove the need for the equivalent of around 3.43 million plastic bottles every year.
Aura3 is a first for the industry and follows other Reliance Medical eco innovations including design changes to ensure 40% more can be shipped in containers to reduce the company’s carbon footprint.
Set up more than 17 years ago, Reliance Medical Ltd employs 68 people in Staffordshire and a further 105 people its manufacturing subsidiary Reliance Medical Shanghai.
Thomas Pear MBA, Managing Director of Reliance Medical Ltd, said: “Reliance prides itself on leading the industry in terms of innovation and thought leadership, supporting and affecting regulatory and legislation changes. Our aim is to continue to grow UK sales and open new export and retail markets around the world.
“Our record-breaking order for over 20,000 AEDs means many more people will be able to easily access these devices - we are proud that each and every one will be there when most needed to save a life.
“2022 was one of our best years in terms of core product sales and at the same time, one of our most challenging, even considering the pandemic in the previous two years. It is down to the goliath effort of our people that we have been able to achieve such impressive results.”
The company has overcome considerable post-Covid supply challenges including a two-month lockdown in Shanghai coupled with industrial action in Felixstowe. As a result almost half a million items including first aid kits were produced in the UK.
In 2022 Reliance Medical opened offices in Ireland and New Zealand. It now has distributors in more than 40 countries and its reach grows year on year. 2022 also saw the company grow its sales on Amazon to supply the whole of Europe with first aid products.
It has a global reach but Reliance Medical is committed to giving back to the local community, including Chairman Andy Pear chairing the charity Ruby’s Fund which supports the families of children with special educational needs and disabilities.
It also regularly donates first aid supplies where needed around the world including recently helping the people of Ukraine and those caught in the earthquake in Turkey and Syria.
Reliance Medical has entered the Business of the Year, Growth and Innovation categories of the Staffordshire University Business Awards.
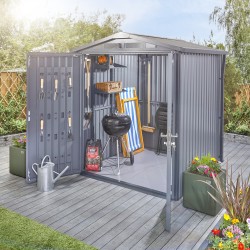
Alpha Manufacturing
Innovation Award entrant
A Staffordshire manufacturing company has launched a subsidiary lifestyle brand after spotting a gap in the market for British-manufactured metal sheds and outdoor living products.
Alpha Manufacturing launched HEX Living in 2022 after supply issues and import problems presented an opportunity to introduce a range of UK-designed and manufactured products to offer buyers an improved experience with more choice, higher quality and readier availability.
All HEX Living products are designed, manufactured and assembled at Alpha Manufacturing’s 80,000 sq ft state-of-the-art facility in Hixon, near Stafford.
A dedicated team of fewer than 10 people are working on manufacturing and promoting the project but they are already gaining traction.
“Being designed and manufactured in the UK gives us a real competitive advantage over competitors whose products are primarily imported from abroad, said Paul Clews, Managing Director of Alpha Manufacturing.
“Thanks to the size of our manufacturing plant, we can manufacture and hold large volumes of stock in Staffordshire. This means we can deliver our products anywhere in the country in just five working days and without expensive delivery charges, providing an excellent purchasing experience for our customers.”
HEX Living has successfully secured major retail partners who list products online and stock in stores. The business also heavily invested in exhibiting at two major trade shows in 2022 – Glee and Solex. Both exhibitions proved successful and generated enquiries and sales.
An articulated trailer has been converted into a mobile showroom, a new storage facility has been built and an e-commerce website has been created for retail customers.
The company has invested in a machine to make custom-designed packaging which it has called ‘a game changer’ for the business as it allows more recycled packaging and reduces the need for single-use plastics.
Paul Clews added: “We’re excited to see where the HEX Living brand goes and the success of the exciting new product ranges being worked on. The Alpha Manufacturing team have really thrown themselves into manufacturing the latest products and it’s great to see the collection going through the facility.”
Alpha Manufacturing is part of the Hex Group that was set up by current CEO Martin Smith’s parents 40 years ago. It has entered the Innovation Award category of the Staffordshire University Business Awards.
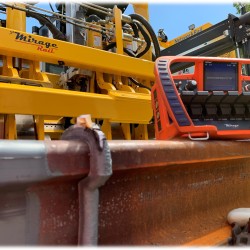
Mirage Ltd
Innovation Award entrant
A Stoke-on-Trent engineering company that started in the garage of its Managing Director now works with some of the biggest automotive companies around the world and its latest innovation is set to be ‘a global game changer’.
Mirage Ltd, which now operates out of a 5.2 acre site in Burslem, specialises in bespoke automated machinery for clients like Toyota, Bentley Motors and Honda.
The team of 18 staff design and build bespoke machinery. They are constantly innovating for their clients and rarely build the same piece of machinery twice.
Network Rail approached Mirage about exploring the possibility of induction welding of rail.
“It is possibly the most exciting innovation the industry has seen in the last 25 years,” said Mirage’s Managing Director, Nick Mountford.
“Network Rail’s current certified methods of joining continuously welded rail are outdated, high risk and potentially dangerous; far from aligned with the care for safety, for community and for the environment that we see elsewhere in the sector.
“Our innovation is a paradigm shift solution that’s set to displace a significant proportion of conventional methods.”
Mirage’s induction welding process is non-sparking and controlled by automotive-industry standard control systems. Rigorous destructive and fatigue testing has shown Mirage’s induction weld is stronger and more resilient to fatigue than the parent material it’s formed from. It’s also super-green with low energy consumption and zero waste to landfill.
Nick says the non-sparking technology has untold potential applications including welding in wet and arid climates, tunnels and underground.
Mirage is already collaborating with heavy haul and mining companies, including with the Australian Rail Track Corporation.
Nick added: “We have a solution that wins for safety, quality and the environment. This is a UK innovation which will be a global game changer. Induction rail welding is a massive step forward for the rail industry.”
Mirage Ltd has entered the Innovation Award category of the Staffordshire University Business Awards.
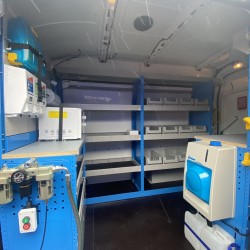
Bri-Stor Systems
Innovation Award entrant
The UK's largest converter of lightweight commercial vehicles, Bri-Stor Systems is constantly innovating to meet its customers’ bespoke needs.
Based in Hixon, near Stafford, the company has 250 employees and is part of the Hex Group that was set up by current CEO Martin Smith’s parents 40 years ago.
Recent innovations include a key-out system that reduces the need for roadside idling and cuts both fuel costs and the carbon footprint of vehicles. This is currently being trialled with several utility companies with the aim of rolling it out.
Simon Webb, Managing Director of Bri-Stor Systems, said: “We have spent the last year working closely with a number of our key partners on this project to deliver a system that reduces engine run time and will reduce fuel costs and the vehicle's carbon footprint. This project has successfully delivered the targets we set out to meet.
“Innovation is at the core of our business and we work closely with customers to quickly understand their specific requirements, developing custom products and solutions where required.”
Bri-Stor’s commercial vehicle conversions include including internal van racking, roof equipment, onboard power and van racking accessories. From design consultancy to manufacture then installation, everything is done in-house.
The company is committed to reducing its environmental impact including becoming carbon neutral by 2037. It’s currently exploring more opportunities with solar power and wind energy with the goal of becoming an off-grid business.
Bri-Stor Systems has entered the Innovation Award category of the Staffordshire University Business Awards.
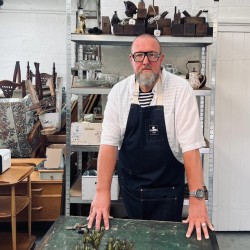
Lost and Found Projects
Innovation Award entrant
International fashion designer Iain Archer has returned to his home city to launch a furniture and interiors business using reclaimed and recycled materials.
Iain did a foundation course at Burslem School of Art and later studied menswear at The Royal College of Art before working around the world for fashion brands including Speedo and Mooks designing street and surf clothing.
He has now founded Lost and Found Projects, a studio and workshop space based within Barewall Art Gallery in Burslem.
Iain redesigns and reimagines abandoned objects such as furniture, fashion, textiles and art, using his skills to turn them into objects people will want in their home. Lost and Found Projects has objects to buy but it is also a studio space where people can watch him working rather than a shop.
Iain moved back to Stoke-on-Trent just before the first lockdown and is committed to being part of the city’s arts scene.
He said: “It was quite a funny feeling coming back to Burslem and walking down streets I hadn’t been down since finishing art college. It’s such a beautiful town with astonishing architecture.
“It’s actually a really creative little hub and we’re trying to help with the regeneration of it.”
Wanting to help regenerate Burslem ties in beautifully with Iain’s passion for ‘circular thinking’ around furniture. “I take things that are redundant for a lot of people and rework them to become an heirloom.”
Furniture was Iain’s hobby during his fashion career and he says he gradually moved into using recycled and repurposed textiles to transform old furniture as a response to trends within the fashion industry.
Most of the pieces currently available at Lost and Found Projects were created by Iain personally but he’s also working on collaborations with other artists.
He plans to have drop-off facilities where people can deposit old fabrics to be reworked rather than sending them to landfill, potentially combined with community workshops.
Lost and Found Projects has been entered into the Innovation Award and Small Business of the Year categories of the Staffordshire University Business Awards.
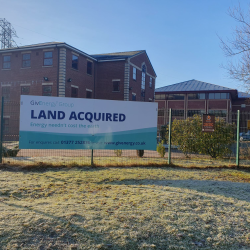
GivEnergy
Innovation Award entrant
The growth of Stoke-on-Trent based GivEnergy has been nothing short of exponential. Turnover has gone from under £1million in 2020 to in excess of a projected £100million in 2023.
Now the business that has only been trading for five years is ramping up its manufacturing capabilities at pace. It is building a new factory in Stoke-on-Trent that’s due to be completed in November, with plans for a second factory pending permission. The company has also bought a new factory in China to keep up with growing demand.
GivEnergy is innovating to end fuel poverty and empower energy freedom for all. Its battery storage systems allow customers to store green energy from renewables and/or from the grid via off-peak tariffs. They can then use that stored energy to cheaply and cleanly power their home or business, cutting both energy costs and carbon emissions in the process.
The company is also giving back by spending around £500,000 per year for the next three years on its not-for-profit business, GivEducation.
“We have the resource to act as a force for good, and we’re passionate about doing so,” said CEO Jason Howlett.
“It’s an exciting scenario: the more we grow, the more we give back to the community, the more we help build a sustainable future, and the more we help mitigate energy security and energy poverty concerns.”
GivEnergy wants to turn North Staffordshire into a centre of excellence for the renewables industry. As part of this, it’s giving back to the communities it serves through continued physical investment. For example, the company has recently brought life back to an abandoned three-story office in Newcastle-under-Lyme – purchasing the property and transforming it into a sustainable HQ that’s completely powered by renewable energy.
“As well as creating new jobs and opportunities for career progression, we also help get people into the work in the first instance, through apprenticeships and graduate schemes,” said Jason. “It’s about giving everyone a chance, no matter what their background.”
Now GivEnergy has entered four categories in the Staffordshire University Business Awards – Business of the Year, Innovation, Growth and Business in the Community.
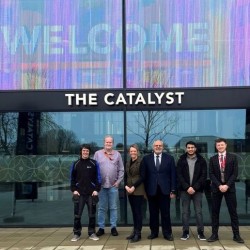
SAS Water Ltd
Innovation Award entrant
A water hygiene company’s latest innovation has been described as a game changer that will transform the water safety sector.
Leek-based SAS Water is working with Staffordshire University to develop a sensor-based solution to automatically monitor water for Legionella bacteria using cutting-edge sensor technologies and a cloud-based management system.
Lizzie Ward, Managing Director of SAS Water, said: “Each year, hundreds of Legionella outbreaks are discovered across the UK and can result in serious illness and death.
“We had an idea for a new product but didn’t have the technical know-how to bring it to market, therefore working with Staffordshire University brings forward a fantastic opportunity to develop a game-changing solution. We believe it will save lives.”
There are more than 500 cases of Legionnaire’s Disease reported to Public Health England in a typical year and studies show the real case numbers are much higher. Legionnaire’s Disease, a potentially fatal form of pneumonia, is much under-reported, so the number of cases is likely to be well over 1,000 per annum.
It is hoped SAS Water’s innovation will improve testing accuracy and save resources and that the company’s partnership with Staffordshire University will help to bring it to market.
SAS Water was founded in 1988 and is an industry leader in Legionella control, working with clients across private and public sectors including factories, councils, nursing homes, housing associations, hotels, spas and leisure centres.
The company’s 14-strong team includes legionella control consultants and commercial plumbers. This mix of staff allows the company to provide a holistic service, supporting new developments from the design and planning phase and throughout a building’s life.
Major contract wins for SAS Water in recent months include Balfour Beatty and Vinci Construction.
The company has a specialist service for hotel, spa and leisure clients and has worked extensively with sports organisations including Burton Albion Football Club.
SAS Water Ltd has entered the Innovation Award category of the Staffordshire University Business Awards.
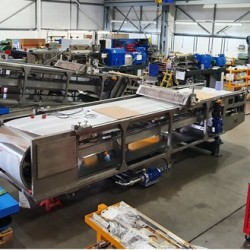
Xtrutech Ltd
Innovation Award entrant
Stoke-on-Trent based Xtrutech was launched in 2002 as a spare parts supplier for other manufacturers and now has its own range, a second headquarters in the US and global sales across Europe, Asia, North America, South America and Australia.
The company has entered both the Innovation Award and Growth Award categories of the Staffordshire University Business Awards.
Innovation is at the heart of everything Xtrutech does and it is currently extending its laboratory facility to accommodate more R&D based projects and trials, including a conference centre where customers can watch the trial and their global colleagues can join remotely.
The team based in Xtrutech’s Stoke-on-Trent headquarters creates bespoke machines for applications that require extrusion as part of their production process. This is adaptable for many different industries including powder coating, biopolymers, medical plastics and more.
In 2021 the company released the first XTS Compactor, a recycling system for use in the powder coating market. A common problem they had observed with their customers was the creation of large quantities of product that is too small to use and is traditionally wasted and sent to a landfill. Xtrutech saw an opportunity to reduce waste, improve resource efficiency and improve environmental impact. The XTS compactor captures the waste, compacts it into a sheet and breaks it into chips. This creates a more substantial product that can be recycled back into production. Based on production averages, using the XTS Compactor can potentially save up to £193,200 annually.
“Our innovations have always been inspired by observing the problems that our customers face and striving to offer a resolution,” said Managing Director Ryan Moore.
In 2020 the company’s export turnover was at 71%, followed by 80% in 2021 and then 93% in 2022.
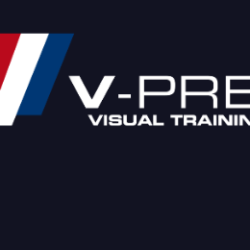
V-Prep IT Ltd
Innovation Award entrant
A Stoke-on-Trent company that creates training videos for pilots has been working with Staffordshire University to develop state of the art, immersive virtual reality software.
Longton-based V-Prep IT Ltd has been making training videos for the Boeing 737NG and the Airbus A320 since it was established by Training Captain James Feeney in 2016.
Now, following a year-long placement by a Staffordshire University VR student, a virtual reality training platform is in the development stage.
“It is our vision to provide quality, cost effective solutions by developing a comprehensive training system which can be used by both individuals and Airline Training Organisations alike,” said V-Prep IT Ltd business development manager Nicky Reeves.
“This style of learning will bring together a symbiotic relationship of visual learning - proven to amplify the learning process and to allow for better overall retention - through our quality training videos and the valuable benefits of innovative, immersive VR.”
V-Prep IT Ltd’s team of eight staff includes animators, videographers, editors and sound technicians to enable all content to be produced in house.
The aim is to replicate the VR training platform for different aircraft and to adapt to the needs of different airlines.
“Currently we are in an alpha stage of the product where we have a comprehensive working proof of concept. We have showcased this to pilots, university students and lecturers to gather fantastic feedback which therefore has aided the development process and ensured the quality and validity of the product,” said Nicky.
Historically pilot training has tended to be via manuals, which are not interactive for users. V-Prep IT Ltd’s aim is to combine theoretical and practical training.
The company has entered the Innovation Award category of the Staffordshire University Business Awards.
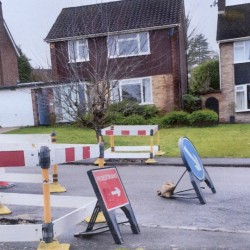
Hayle Communications
Innovation Award entrant
A moling machine, capable of installing new and replacement underground ducts and services quickly and efficiently, has a potential worldwide market when it goes into production later this year.
The electrically-powered device is the brainchild of communications installations engineer Bill Mabey and has been worked on by students in Staffordshire University’s Innovation Centre.
Bill hopes the machine will go into production within the next few months, through his company Hayle Communications, and believes it will have a dramatic impact on the sector including significantly reducing the need for pothole repairs.
Bill said: “The machine is electrically operated and fitted with a tracking system to enable accurate installations.
“Being silent it is suitable for use in urban areas at night when traffic levels are low and avoids costly trenching and reinstatement, which is one of the causes for creating potholes, which then damage vehicles, resulting in constant and expensive repairs to vehicles and road surfaces.
“There is a high worldwide demand for moling machines for installing new and replacement utility services to homes. Machines currently on the market are noisy, air operated and there is a restricted moling range of around 100 feet for use only in temperatures above zero.
“Our Electric moling machine is silent, compact, transportable in a small van and eco friendly.”
Bill has been working with Staffordshire University students on a tracking system for the moling machine and on switching the machine’s power source from petrol to electric.
He has now entered his moling machine into the Innovation Award category of the Staffordshire University Business Awards.
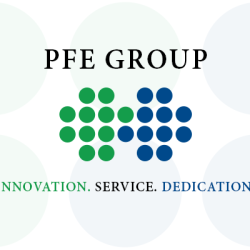
PFE Medical
Innovation Award entrant
A Stoke-on-Trent company has a developed and patented a piece of medical kit that could save lives around the globe.
PFE Medical, based in Fenton, has been working on the world’s first automated endoscope cleaner, called The Khamsin.
The first Khamsin is set to go into use in a hospital in Birmingham in spring to summer of this year.
PFE Medical is now working on a manufacture under licence agreement and aims to roll the kit out worldwide later this year.
Rob Hartley, Director and Founder of PFE Medical, says there are 450 endoscope units in the UK and approximately ten times that number in both Europe and the US. The Khamsin has the potential to revolutionise working practices in all of those.
He said: “It’s fairly well acknowledged that endoscopes are very difficult to clean and disinfect. People have been trying to find a way to clean them automatically for 40 years. We have patented that.”
Rob, who originally trained as an accountant, set up his company in 1990 and now has more than 40 staff and a multi-million-pound turnover.
He explained: “The Khamsin utilises nano-particles and ultrasonics to create oxygen bubbles on all of the surfaces of the endoscope. The implosion of these is 100% effective in removing both protein and pre-existing biofilms. The Khamsin would replace the manual cleaning of endoscopes thus benefiting the three million patients that have endoscopies each year in the UK.
“At least 32 multi-drug resistant organisms were found in 400 patients between January 2000 and January 2017 with 20 deaths; between October 31, 2018 and March 31, 2019 there were three deaths, 45 infections and 159 device contaminations due to inadequate reprocessing of duodenoscopes in the USA.
“The Khamsin is the only automated endoscope cleaner currently on the market, which eliminates human error as currently endoscopes are cleaned manually. The whole decontamination process is fully validated and is environmentally friendly.
“The cleaning efficacy is 100% effective on every endoscope for every patient, multiple successful tests have been completed on numerous bacteria and fungi, including Pseudomonas Aeruginosa and Escherichia Coli.”
PFE developed the Khamsin during a three-year knowledge transfer partnership with Aston University.
The company is also now working with both Staffordshire and Keele Universities including placements for two Staffordshire University students to work on R&D and marketing for the Khamsin.
Rob has now entered his company into the Innovation Award category of the Staffordshire University Business Awards.